Penetrant testing by experts – inspection options from a single source
Advanced penetrant testing for cost-efficient precision in material inspection
We detect surface defects with high accuracy, quickly and reliably
At VCxray Inspection Services, you will find a comprehensive inspection center: as a service provider, we offer penetrant testing (PT), also known as dye penetrant testing or red-white testing, in addition to other inspection methods. This is a fundamental method of non-destructive testing (NDT) that is used in almost all industries.
With our specialized stationary and mobile equipment, you can rely on our team to carry out thorough inspections. These help you to detect surface defects such as cracks and pores in critical components and to prevent material failures that could lead to costly downtime, reduced safety or catastrophic consequences.
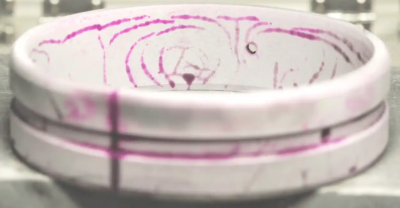
Dye penetrant test of a bearing ring
Photo: Helling, Heidgraben
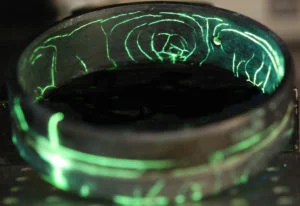
Fluorescent penetrant testing of a bearing ring
Photo: Helling, Heidgraben
Our service:
We use penetrant testing to help you detect defects that cannot be seen with the naked eye. This is how we ensure the highest quality, reliability and safety for your critical components.
The tests are carried out by qualified, certified personnel according to DIN EN ISO 9712 levels 2 and 3 and/or qualified personnel according to DIN EN 4179 levels 2 and 3. We comply with DIN ISO 3452-1; this is mainly used for metallic materials, but can also be carried out on other materials, provided they are not excessively porous (castings, forgings, welds, ceramics, etc.).
Our penetrant testing services include manual testing at our premises or on-site at the customer’s for large components and semi-automatic testing for smaller parts and larger quantities.
We use two proven methods to meet your specific requirements: fluorescence penetrant testing under UV radiation for increased sensitivity and classic penetrant testing (red-white) for components with lower requirements, for example.
How your business can benefit from penetrant testing
Penetrant testing is an essential solution for industries such as aerospace, automotive and manufacturing to find surface defects.
Versatility
⇒ Suitable for a wide range of materials including castings, forgings, ceramics and welds.
High sensitivity
⇒ Detects even the smallest surface defects, ensuring the quality of critical components.
Simplicity and speed
⇒ Quick to perform with uncomplicated, easy-to-interpret results.
Cost efficiency
⇒ A highly economical solution for comprehensive material testing without compromising on quality.
PT inspection procedure

- Contaminated test piece: The part may be contaminated and must first be prepared for the test.
- Pre-cleaning: The surface of the test piece is thoroughly cleaned to remove contaminants such as rust, grease or scale.
- Application of penetrant: A coloured or fluorescent penetrant is applied evenly to the surface.
- Intermediate cleaning: Excess penetrant is carefully removed from the surface without removing it from the imperfections
- Drying: The surface is dried to remove residual moisture
- Application of the developer: A white developer is applied to the dry surface
- Development time: The developer draws the penetrant remaining in the defects to the surface
- Inspection: The surface is visually inspected for signs of defects, which appear as coloured marks on a white background
Contact our experts to discuss your projects – we will be pleased to support you in your testing tasks.